Well I’m trying to keep myself busier on weekends.
I did my 7 mile morning run with my running class. I ran with a good crowd including Chris, Jay, Robert, Celeste, and Glenn. We chatted all the way which was nice. This class and my running continues until next February’s Austin Marathon. Wish me luck. I need it.
After arriving home I cleaned-up and then I added 1GB of RDRAM to my son Matthew’s old Dell Dimension 8100. I had purchased this memory on e-Bay last week. The memory was not cheap, but the machine is a 1.3 GHz Pentium 4 which is better than my old 800 MHz AMD Athlon that I had disk nuked a week or so ago. Next I installed Linux Fedora 7 on it, and I installed some work things (Cell Broadband Engine Software Development Kit) on it too. Now it’s ready to go and with the additional memory the machine is quite snappy so it was a worthwhile purchase.
I again continued to reduce Lego entropy. Earlier this week I sorted, and inventoried the 8854 Power Crane.
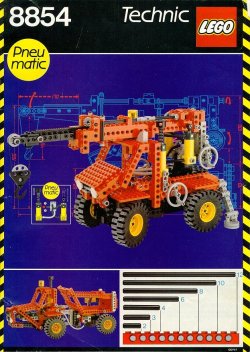
Image courtesy of brickset.comThanks to
peeron.com for the inventory list. I printed out a copy of the inventory and cut it up it into strips contains a related group of parts. For each group I put the cut up strip into a snack-size baggie, found and counted the parts into the baggie, and put the now filled and sealed baggie into a larger gallon-size baggie. For this kit I am missing only three parts. Now the question is: where can I get them?
Then I sorted the hundreds of miscellaneous parts (non-blocks or plates) into groups and put them into baggies. I really need several containers with little divided sections.
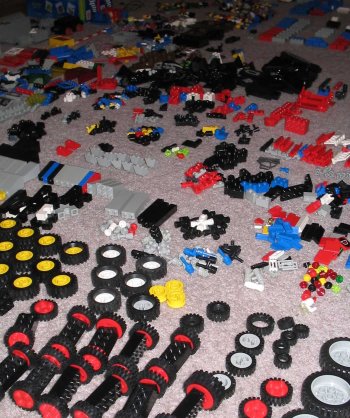
This might look messy and totally disorganized, but actually it isnt’t. Each bunch is a group of the same type of piece regardless of their colorUpdate: My friend Larry P. told me that you can get Lego blocks from
bricklink.com. The site says “BrickLink.com is a premium venue for individuals and businesses from all around the world to buy and sell new, used and vintage LEGO® through fixed price and auction services.”